Microgravity Enabled Paddle Wheel
Testing at NASA
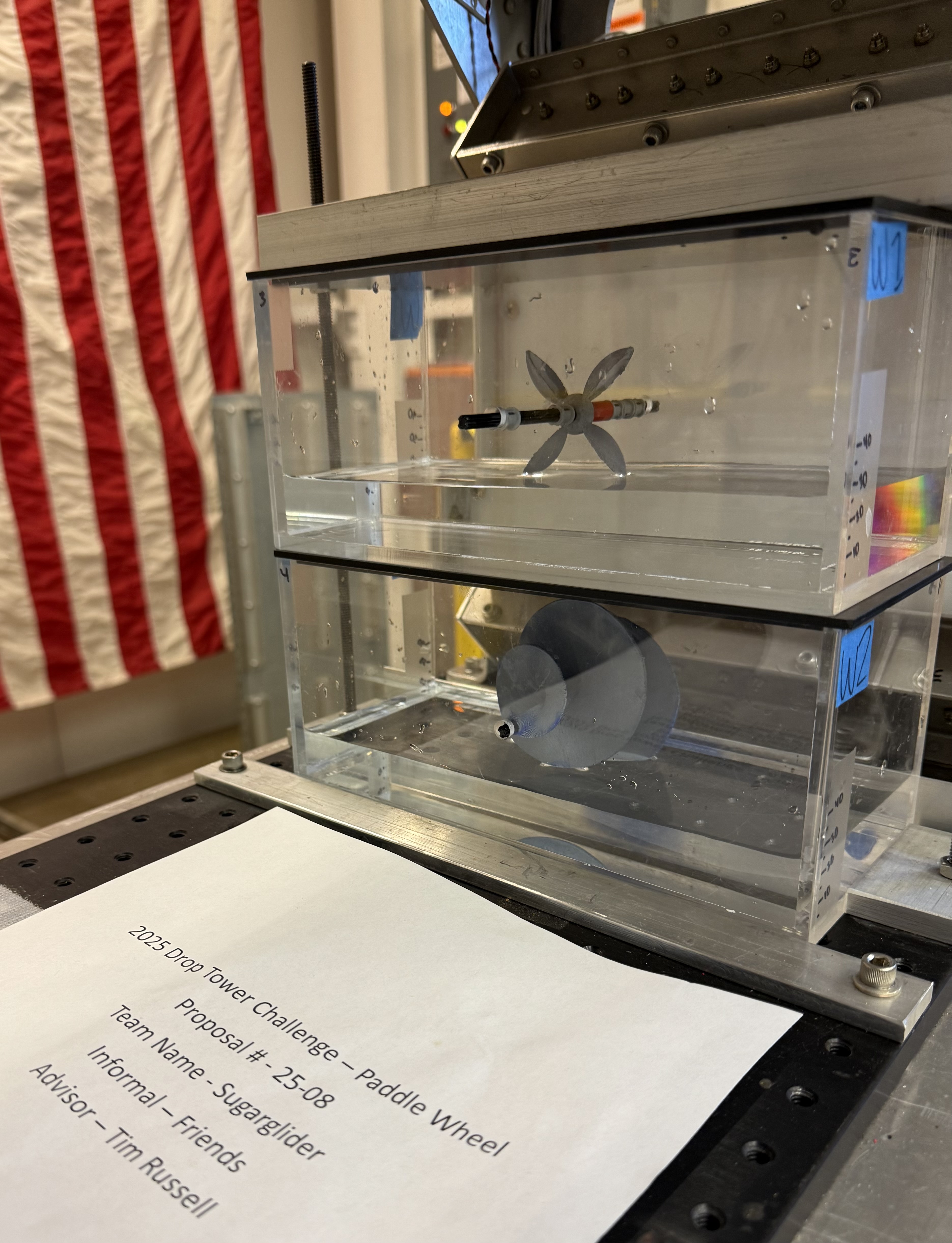
An experimental study on two 3D-printed paddle wheel designs, tested in a custom microgravity drop tower to evaluate rotational performance under free-fall conditions.
1. Project Overview
We fabricated two PLA paddle wheelsâa classic straight-blade and a spiral variantâand applied a hydrophobic top coat to each. The goal was to see if passive interfacial forces alone could overcome axle friction under microgravity. Despite multiple drop tests, neither design achieved sustained rotation, revealing critical torque limitations.
2. Objective
Determine if capillary and hydrophobic/hydrophilic interactions can generate continuous rotational torque on a paddle wheel during ~1â2 seconds of free-fall.
3. Methodology
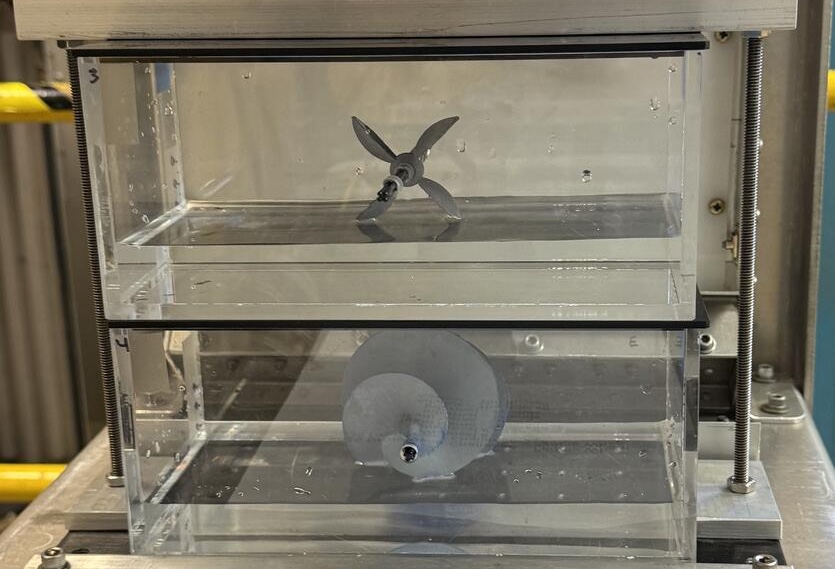
- 3D-printed two paddle wheel geometries in PLA.
- Applied a gray primer and hydrophobic Rust-Oleum NeverWet coating.
- Built a transparent water chamber around a low-friction axle.
- Recorded each drop (7 m & 24 m) with a high-speed camera, varying water depth (25 mm â 35 mm).
4. Results & Findings
- The straight-blade wheel rotated only ~15° transiently; the spiral design remained motionless.
- Calculated interfacial torque was insufficient to overcome bearing friction and inertia.
- Longer free-fall (24 m) did not improve engagement, underscoring the need for higher initial torque or active mechanisms.
5. Next Steps
- Redesign blade geometry to amplify capillary forces (e.g., angled or asymmetric vanes).
- Incorporate low-friction magnetic or air bearings to minimize resistance.
- Explore active fields (acoustic, electric) to kick-start rotation in microgravity.
Key Features
- 3D printed paddles
- 3D modeling
- hydrophobic coatings
- Microgravity testing
- High-speed video analysis
Technologies Used
Research Documentation
PaddleWheel Research Paper